The
ultrasonic generator generates 15KHz high-voltage and high-frequency electrical signals, which are converted into mechanical oscillations of the same frequency through the piezoelectric inverse effect of the transducer, and act on the plastic workpiece in the form of audio longitudinal wave. Through the friction between the surface of the workpiece and the internal molecules, the temperature transmitted to the joint increases. When the temperature reaches the melting point of the workpiece itself, the workpiece interface melts rapidly When the vibration stops, the workpiece is cooled and shaped under certain pressure to achieve perfect welding.
4、 Main structure and component brand of the equipment:
4.1 energy exchange system: the chip transducer made in Japan and the Japanese Imperial steel horn are used. The power is strong, firm and wear-resistant, and the power is 20% higher than that of the same domestic energy conversion system.
4.2 pneumatic components: the well-known brand large-diameter cylinder Φ 63 * 80mm-20, five-way solenoid valve, smooth up and down operation, good buffering effect, eliminating the impact force of welding head on the workpiece and the back impact on the transducer, which is more conducive to welding more precise workpiece and effectively protecting piezoelectric ceramic plate.
4.3 the machine is equipped with a precise fine adjustment mechanism, the fine adjustment distance can be as precise as 0.02mm, and there is an instrument indication. The height of the machine body and the falling distance of the welding head have scale indication, and the accuracy is 1.0 mm;
4.3 rack: unique rectangular column design, higher mechanical strength, effectively avoiding the phenomenon of backward tilt when working. The frame sheet metal is all processed by laser cutting machine and CNC plate cutting and bending machine, which ensures that the assembly of the whole machine is well matched, and the whole machine is painted, with good adhesion, no falling off and beautiful appearance.
4.4 motion structure: the equipment adopts Taiwan linear slide rail with high precision (which is incomparable with traditional guide rod and linear bearing) and is solid and wear-resistant, which makes the welding head drop more stable and does not shift. It is more conducive to welding more precise products.
4.5 balance mechanism: the transducer assembly can rotate freely, and the transducer assembly is provided with a horizontal adjustable structure, and the workbench is provided with an adjustable structure. The two debugging structures make the debugging mold more convenient and quick, easy to operate and easy to learn and understand
4.6 electrical system: a complete set of high-quality imported components are assembled, and the power amplifier part is improved in design, and the amplification components are added to share the load,
It can reduce the temperature rise of the triode and reduce the damage rate. There is no program control board design. The Japanese Omron time relay replaces the mechanical time dial switch, so the time control is more accurate and reliable.
Type |
Power(W) |
Frequency (KHz) |
PU-UWM600W |
600W |
15KHZ/20KHZ/28KHZ/40KHZ |
PU-UWM900W |
900W |
15KHZ/20KHZ/28KHZ/40KHZ |
PU-UWM1000W |
1000W |
15KHZ/20KHZ/28KHZ/30KHZ |
PU-UWM1500W |
1500W |
15KHZ/20KHZ |
PU-UWM1800W |
1800W |
15KHZ/20KHZ |
PU-UWM2000W |
2000W |
15KHZ/20KHZ |
PU-UWM2600W |
2600W |
15KHZ |
PU-UWM3200W |
3200W |
15KHZ |
PU-UWM4200W |
4200W |
15KHZ |
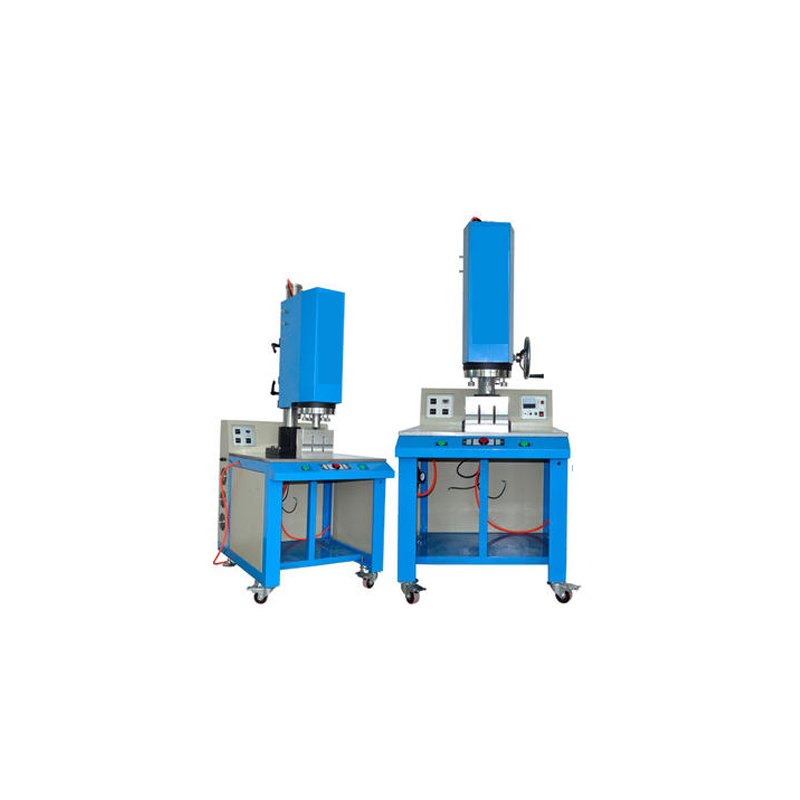
Consult immediately